Engineering and Product Design Services
Our engineers are experts at ensuring that we continually provide the best manufacturing solution possible for every product. We achieve engineering optimization through improvements in design-for-manufacturability (DFM) and lean manufacturing processes. In addition, our engineers design and produce the most effective methods to handle and/or trim your products. We design the equipment as well as the process to ensure every quality part is produced to the same exacting specifications.
Polyfab LLC’s dedicated engineering department can coordinate and expedite injection mold maintenance, repairs, and revisions to streamline the continued production of your products. Our collaborative engineering team regularly holds project review meetings with our clients – beginning in the design/prototyping stages and continuing through to manufacturing and delivery – ensuring absolute satisfaction with the product.
In many cases, our highly involved engineering solutions are instrumental in the long-term success of our customers’ projects.
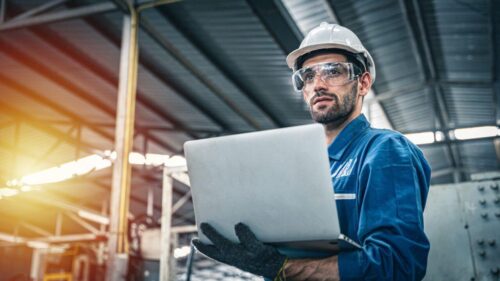
Injection Molded Product Engineering Services
- Material evaluation
- Product design support
- Feasibility and optimization studies including mold, process and automation evaluation
- Advanced quality planning
- Total program management from concept to production
- Design for manufacturability
- Product enhancement
- Cost improvement
- Kistler and RJG in-mold instrumentation and process control
The Polyfab Engineering Process
Our process includes integrity, innovation, and solutions. This means Polyfab is committed to give you the most ethical, quality conscious partnership possible. By using the most advanced equipment coupled with the creative, professional team we have assembled, you are assured products that will exceed your expectations.
An Overview of Our Product Engineering Process
- Evaluation of idea and concept.
- Review of product design for manufacturability and sustainability.
- Assist in material selection after application review.
- Design the custom mold for proper cavitation based on product forecast.
- Build the mold utilizing 3D CAD and mold fill simulation software.
- Sample the mold in a production press for customer approval.
- Set up a rigorous molding sample run to ensure a stable production process.
- Establish production part approval process – PPAP.
- Monitor production and maintain that all parts and processes remain in accordance with all customer specifications.
Custom Automation and Robotics – Automated Injection Molding Solutions
In many applications, Polyfab can engineer a custom automation solution for injection molding that minimizes hands-on involvement and labor requirements. Simultaneously, our automation solutions result in improved product quality, consistency, repeatability, and ultimately creates the best value for our customers and their products.
We comprehensively engineer our automation solutions through an early evaluation of the product requirements, looking for any opportunities for process improvements. Our experienced automation engineers on staff to design and manufacture optimum interfaces and equipment for your product needs. We offer extensive hands-on knowledge of a wide variety of automated secondary operations including trimming, assembly, and flexing living hinges before packaging.
Our Scientific Approach to Product Engineering and Problem Solving
The molding process is developed using a systematic, data driven approach. Those conditions that prevent necessary process control are first identified and corrected. Then, a robust, repeatable process can be established and defined by meaningful plastic conditions, independent of machine settings.
Polyfab is staffed with a Master Molder Certified Process Technician on every shift. Communication between technicians takes place using common terminology regarding specific process inputs and outputs. Because of this, problem solving is a systematic procedure structured around defining the root cause, with actions taken based on knowledge of the process.
Some of the tools Polyfab uses to drive process control and improvement through meaningful data include:
- Kistler cavity pressure sensing.
- Our dedicated team of highly skilled employees use meaningful data to drive process controls and improvement.
Product Development Services
- Assistance with custom product design, including assistance in design for manufacturability (DFM).
- Complete product development support – from prototyping to production.
- Material procurement and source or supply assistance.
- Feasibility and optimization studies of mold design, production processes, and custom automation solutions.
- Advanced quality planning.
- Overall product enhancement.
- Evaluate potential cost reduction options.
- Collaborative project review meetings with customers throughout the entire manufacturing process.
- Coordinate and expedite any revisions, mold maintenance or repairs.
- Evaluation of custom fixtures necessary for each unique product.
Product Design Review / Design for Manufacturability (DFM)
- Application-specific design solutions.
- Cost evaluation and optimization.
- Marketability and industry analysis.
- Analysis of annual projected product volume to determine optimum cavitation and press size.
- Prototype design and manufacturing assistance utilizing single cavity mold.
INNOVATIVE ENGINEERING SOLUTIONS FOR THE AMERICAN INJECTION MOLDING INDUSTRY SINCE 1971
Polyfab is one of the plastic injection molding industry’s leading engineering and manufacturing companies. We strive to provide the best products possible, backed by the most efficient and sustainable production processes available for each application. Based in Sheboygan, Wisconsin, our company has delivered innovative American engineering solutions for more than half a century.